Recent world events have made things very tough for manufacturers. Many jobs can be done from home, but if your employees have to use your tools, they need to work in-house. However, being flexible concerning workflow, schedules and communication can make it easier to get your entire team on board from within your facility.
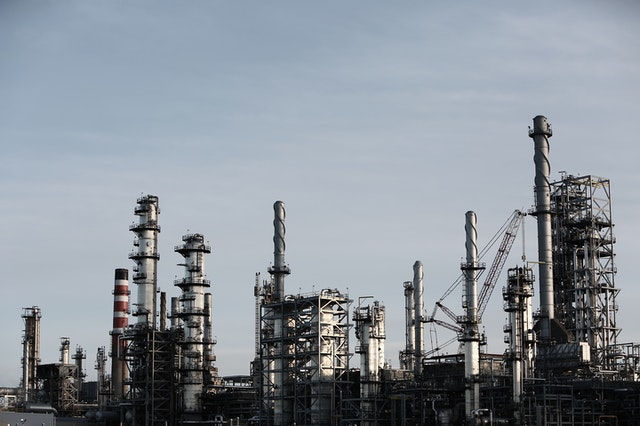
Engage All Employees with Customizations
Many factors in the manufacturing process work well from the outside but do not serve the people doing the work. For example, a well-balanced manufacturing workspace with equal access to all necessary tools can look well-organized, but what works well for a right-handed employee may not be as useful for a left-handed employee.
Options for customization within their workspace can do a great deal to increase employee engagement. These customization factors can include
- height adjustments
- reach adjustments
- storage customization tools
- rear vs. side exposure
If your facility is particularly loud, make sure that you have easy options to move away from noisy tools for a quick conversation.
Offer Schedule Flexibility
As noted above, your manufacturing employees can’t work from home. However, you may be able to make upgrades to security to allow your team members to work more flexible hours. For example, you may have employees who need to be home by three because after-school programs are not available or consistent.
To avoid the challenges they would face trying to stick with a 9 to 5 schedule, consider what they can do in your facility if they can start at 6 or 7 a.m. You could find that by offering this flexibility you can
- increase loyalty
- boost employee engagement
- tap into their most productive time of the day
Going the extra mile to allow an employee to make their life work is one of the best ways to increase employee buy-in. An employee who feels heard and valued will bring their best ideas to the table.
Audit the Process
Some employees easily see connections from one worker to the next, from one department to the next, and from your raw good suppliers to your facility. This employee is a great candidate for vda 6.3 process audit training. Once fully trained, an employee who can conduct a process audit can review internal processes before you make a product line change.
An internal auditor can also be extremely helpful when it is time to add new tools, add another shift, or if you get a batch of new employees. Your auditor may be part of your QC team or part of HR. Solid knowledge of material routing through your facility is key to an effective audit.
Train Consistently
There are things that all employees need to know to function in your facility. Few manufacturers sell directly to the customer without having to meet some quality standards across the industry. The first step to building your training program is to make sure that said training is closely tied to meeting these standards.
Because not meeting these standards can impact your rating as a manufacturer and cut into your bottom line, standardized training with some hard and fast rules will protect both you and your employees. An easy place to start is with safety gear. If goggles and ear protection are required, everyone has to have that gear, and ignoring that requirement can be a reason for disciplinary action no matter the longevity or level of that employee.
Make Preventive Maintenance Part of Your Process
A simple way to include your employees in “bottom-line thinking” make preventive machine maintenance part of the process. If any employee notices an issue with a machine and you can make a simple repair that prevents a costly repair or replacement, celebrate it! Catching these situations before they become huge expenses and sharing that success is another way to promote engagement.
Your employees can become your partners in process improvements. Training someone to fully audit your processes when it’s time to ramp up production, change a product line, or add a shift can prep your whole team for a more profitable business.