As a business distributor, ensuring products’ protection and preservation is paramount. Distributors must take all necessary steps to ensure their products’ safety from external and internal threats. In doing so, distributors can reduce the risk of lost effects and ultimately benefit their business’s bottom line. Here are tips on how to best protect products as a business distributor.
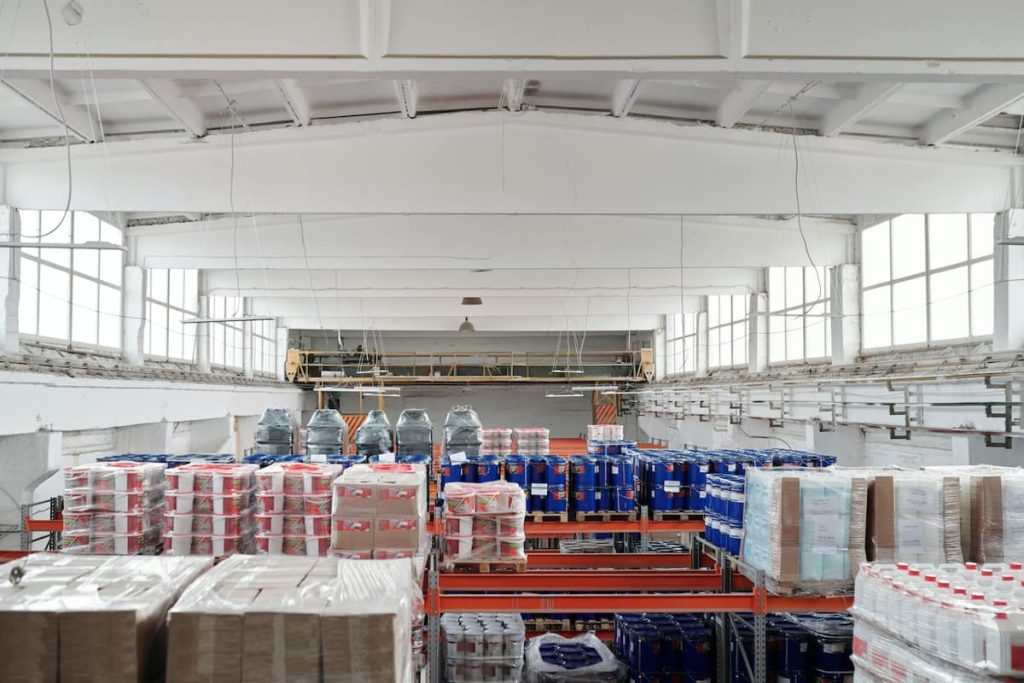
Inventory Tracking System
Distributors can supervise the quantity and location of their product lines at whatever time by using an inventory tracking system, which lowers the possibility of potential losses from theft or accidental shipment. Additionally, it enables distributors to precisely track orders and spot any inconsistencies in turnaround or delivery times.
Advantages of an Inventory Tracking System
Distributors can gain from an inventory tracking system in several important ways, such as improved inventory management, improved order fulfillment, decreased inventory losses, and enhanced customer service.
Ways to Implement an Inventory Tracking System
Distributors can implement an inventory tracking system using various software, hardware, or manual methods. Such methods include barcode scanners, RFID chips, and point-of-sale systems. Other methods include tally sheets, checklists, and physical inventory counts.
Record Keeping & Insurance Coverage
Distributors should keep detailed records of incoming shipments, outgoing shipments, inventory counts, order histories, customer data, and other pertinent information about their products and services. Moreover, distributors should also consider purchasing insurance coverage for their products to protect themselves if something unexpected happens.
Monitor Products during Transit
Monitor products during transit if possible. This can be done through advanced tracking systems and visually inspecting packages before shipment for any potential damage or defects that could affect product quality when it reaches its destination. Monitors should know how containers were stored before shipping and any potential environmental factors that could affect product quality during transit times.
Secure Storage Facilities
The first thing is to ensure products are stored in secure storage facilities, such as a warehouse or self-storage facility. Self-storage facilities provide a great way to store products securely because they are typically climate-controlled and monitored around the clock. To further protect your products, you may also consider purchasing self-storage facility insurance, covering damages and losses associated with floods, fires, and other natural disasters.
Train Employees on Security Protocols Processes
Another way to protect products as a business distributor is to train employees on security protocols and processes. Distributors should consistently train their employees on how to store correctly and transport products safely so that no mistakes are made. Furthermore, it is also vital for employees to understand the company’s security protocols in case of an emergency to react quickly and efficiently.
Ensure Hiring Practices are up-to-date.
Distributors need to ensure their hiring practices are up to date regarding protecting products as business distributors. It’s essential that only trained staff handle product shipments and that each employee has been thoroughly vetted before being hired to minimize the risk associated with negligent employees or dishonest workers attempting to steal valuable goods or services from your organization.
Securely Vet Potential Employees
A secure vetting process for potential employees is vital to ensuring that hiring practices are up-to-date for product distributors. This should include background checks, in-person interviews, and other measures necessary to verify the trustworthiness of individuals looking to be hired.
Provide Adequate Training
Providing staff with adequate training on handling product shipments is also essential to protect valuable goods and services from being stolen or mishandled. Training should cover safety protocols, storage, and handling requirements, and protocols for reporting suspicious or unauthorized activities. It should also include a comprehensive explanation of the company’s policies and procedures.
Follow Package Logistics Rules
Observing package logistics regulations is the third piece of advice. Specific procedures that must be followed when shipping packages from one location to another are called package logistics rules. These guidelines, intended to protect packages during transit, should always be complied with. For instance, many businesses demand distributors use reliable packaging supplies and double-check package addresses before sending out goods. Ensuring the Parties Included.
Package Logistics Rules
- Use Reliable Packaging Supplies
- Double-Check Package Addresses
Ensuring the Parties Included
- Verify the Designated Recipient’s Name
- Check Shipping and Billing Addresses
- Include Instructions for Delivery Personnel
Utilize Technology & Automation
Technology can help streamline the process of shipping orders and tracking inventory levels more efficiently than ever before. Automation can also significantly reduce human errors when entering data about shipments or following inventory levels, preventing costly mistakes down the line.
Conclusion
Protecting products as a business distributor requires diligence and a comprehensive approach that incorporates secure storage facilities, an inventory tracking system, necessary package logistics rules, security cameras, insurance coverage, verified third-party providers, technology automation tools, monitors during transit times, and up-to-date hiring practices. Adopting these measures can help distributors safeguard their goods from internal and external threats while keeping their bottom line healthy in the process!