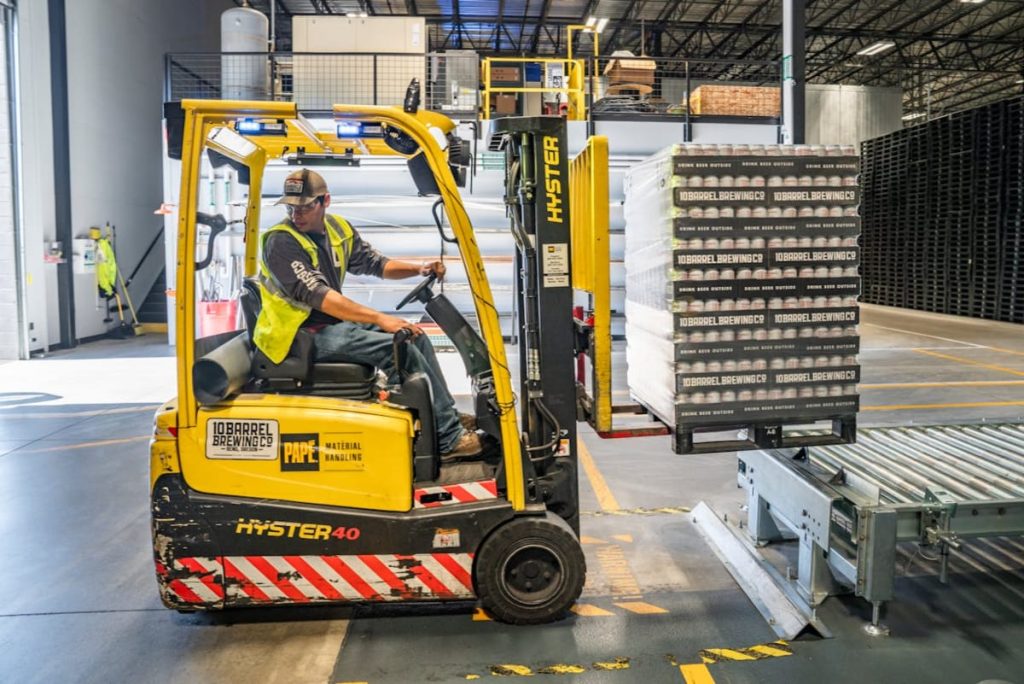
Warehouse settings are buzzing hubs of activity where output and efficiency works. Maintaining safe working conditions in a warehouse goes beyond following rules; it also requires building a culture in which safety permeates all facets of operations. Warehouse officials can greatly lower the risk of mishaps and injuries by concentrating on preventative actions, staff education, and regular evaluation of processes. Six basic safety tips which are vital for preserving a safe warehouse environment will be explored in this article.
Proper Training and Education
Providing adequate training and information to all personnel regarding any hazards they can encounter is a critical component of warehouse safety. Every newly employed worker should be obliged to engage in extensive training courses, including machinery operation, handling of personal protective equipment (PPE), and methods of lifting and moving heavy objects. Since it keeps workers updated on the most recent safety practices and procedures, ongoing education is also rather vital. Emergency response protocols, such as what to do in a fire, spill, or other hazardous situation, should also be taught in training. Workers who are familiar with safety procedures are more likely to make wise judgments meant to stop mishaps.
Maintaining Clear and Organized Workspaces
A well-organized workplace also helps machines run smoothly and lowers the possibility of mishaps brought on by lost objects. Frequent inspections help to guarantee that every part of the warehouse is kept neat and that any possible risks are quickly handled. Tools and supplies should also be kept in specific areas, and staff members should be educated to put objects back where they belong following usage. By precisely pointing out where goods should be kept and where hazards might present, labels and signs help to preserve this order. By encouraging a culture of organization and cleanliness, warehouse officials can drastically lower the likelihood of mishaps and establish a more effective workplace. This improves efficiency as well as safety since employees can more quickly locate the tools and supplies needed to do their jobs.
Emergency Preparedness and Response
Emergencies can strike at any moment; hence, lessening their consequences calls for planning. Every warehouse should have a thorough emergency readiness plan covering procedures for several events like fires, chemical incidents, and natural disasters. Every staff member should be familiar with this approach; regular exercises will help to ensure that everyone knows what to do in an emergency. Consulting skilled floor coating contractors is crucial for ensuring staff safety and reducing the chance of slipping. Proactive and well-prepared warehouse authorities help lessen the consequences of emergencies, protecting assets and people.
Implementing Safety Signage and Floor Markings
Effective communication is essential in any safety program, and one of the greatest methods to communicate safety information in a warehouse is through signs and floor markings. Safety signs should be positioned deliberately throughout the warehouse to alert staff members to possible hazards, such as regions where heavy machinery is running, areas with lots of foot traffic, or places where dangerous chemicals are kept. By defining walkways, marking off limited areas, and directing traffic inside the warehouse, floor marks can also be rather important for preserving safety. These visual signals are crucial for avoiding mishaps since they give staff members clear directions and warnings, therefore guiding them across the workplace securely.
Regular Equipment Maintenance and Inspections
Equipment and tools, such as conveyor belts and forklifts, are essential to warehouse operations. Although these instruments are necessary for output, improper maintenance of them can cause major safety hazards. Finding possible faults before they become major concerns depends on regular maintenance and inspections of all equipment. Establishing preventative maintenance plans will help to guarantee that every machine is routinely repaired, therefore lowering the risk of mechanical breakdowns causing mishaps. Employees should also be taught to spot equipment faults and notify others right away.
Proper Use of Personal Protective Equipment (PPE)
A key component of warehouse safety, personal protective equipment (PPE) offers the last line of defense against occupational hazards. Employees require the correct PPE for their specific occupations, whether it means high-visibility vests, gloves, safety goggles, or hard helmets. Staff members should be urged to report any equipment problems right once and to always wear their PPE in approved areas. Regular audits help to guarantee adherence to PPE guidelines; supervisors should set an example by regularly donning their protective gear and mandating its use among staff members. Warehouse official can greatly lower the risk of harm by giving the correct use of PPE priority, therefore providing a safer workplace for all those engaged.
Conclusion
Safety in warehouse settings is not just a legal need but also a basic need for preserving a good and efficient workstation. Warehouse officials can make the workplace safer for every employee by concentrating on these six basic safety tips: appropriate training, keeping orderly workspaces, employing safety signage, regular equipment maintenance, correct PPE use, and emergency readiness. Every one of these suggestions is very important in lowering the possibility of mishaps and guaranteeing that employees can carry out their jobs safely and efficiently. A dedication to safety not only shields workers but also helps the warehouse to be generally successful since a safe workplace allows employees to concentrate on their responsibilities free from concern for injuries.