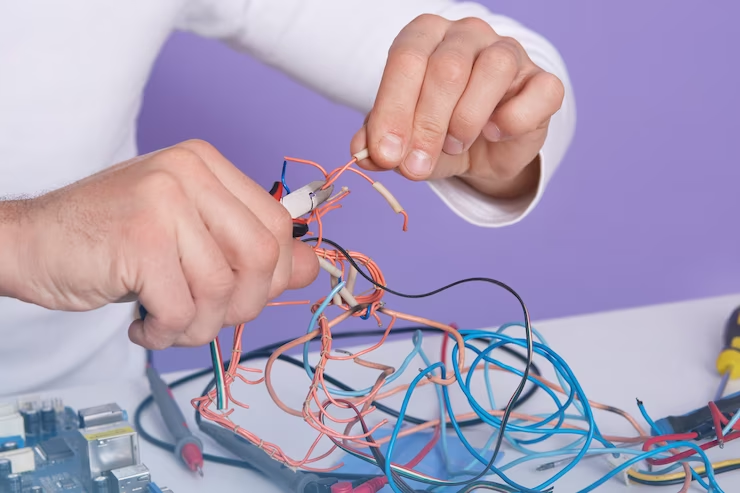
A wire harness is a methodical and integrated arrangement of cables inside an insulating material. It is also known as a cable harness and wiring assembly. The assembly’s function is to convey electrical power or a signal. Straps, conduits, sleeves, cable lacing, electrical tape, cable ties, or a combination bind these cables together. The wiring is combined into a single unit for “drop-in” installation in the wire harness, which makes connecting to larger components simpler.
You can produce products that meet the requirements for international quality by learning the necessary international standards, norms, and requirements, as well as compliance guidelines, through the IPC 620 Certification Program. You will be able to complete all cable and wire harness assemblies with practical expertise.
Cable Assemblies Versus Wire Harnesses
Although the two are very different, wire harnesses and cable assemblies are frequently confused. The primary distinction is that a wire harness comprises several breakouts (ends) that extend in many various directions and have numerous terminations on every breakout, while a cable assembly typically only has two ends.
The majority of the time, wire assemblies are found in vehicles, including cars, buses, trucks, and airplanes. Wire harnesses will also be used to construct industrial machinery, electronics, white goods (home appliances), and construction machines.
Benefits of Wire Harness Assembly
Shortened Installation Period: Many autos need miles of wire to function. The construction of these vehicles is significantly streamlined by a wire harness assembly technique that incorporates all necessary wires and cables into a single device. Instead of running each wire individually, installation is as easy as “dropping in” the harness.
Security and Safety: Individual components are better protected from the damaging effects of vibrations, abrasions, and wetness when wires and cables are bonded within a single harness. The wires have been built into a non-flexing bundle, which maximizes space and lowers the possibility of an electrical short. When the wires are contained inside a flame-resistant sleeve, the chance of an electrical fire is also decreased.
Design and Pre-Production of Wire Harness
A wire harness method is created according to the structural and electrical specifications of the machinery it will be put in. A schematic is then used to produce the product documentation and the assembly board for the harness after the initial design has been decided upon. The assembly board, also known as a pin board, is a full-size schematic of the harness that displays every component and where it is located. It also functions as the harness’s workbench.
Process for Manufacturing and Assembling Wire Harness
The harness wires are first cut to the required length and labeled properly. The uninsulated conductor is exposed at the wire ends, and any necessary terminals or connection housings are fitted. The wires and components are then put together on the pinboard according to the appropriate specifications before being bonded.
The Reason Wire Harnesses Manually Assembled
Wire harness assembly is one of the few manufacturing operations that can still be performed more effectively by hand rather than by automation. This is a result of the assembly involving a wide range of operations. Among these manual procedures are:
- Putting in terminated wires of different lengths
- Putting cables and circuits through conduits and sleeves
- Record breakouts
- Carrying out several crimps
- Using cable ties, tape, or clamps to bind the parts together
Since automating these processes is challenging, manual production is still more economical, especially for small batch sizes. The fabrication of harnesses takes longer than the production of other cable assemblies for the same reason. It can take a few days to many weeks to complete a project. The longer production times are necessary, the more complex the design.
However, some pre-production processes could use a degree of automation. These consist of the following:
- Cutting and stripping individual wire ends with an automated machine
- Crimping terminals on either or both wire sides
- Insertion of wires with terminals pre-installed into connection housings
- Wire ends are soldered
- Bending wires
Testing of Post-Production Wire
Testing the harness for electrical operation is the last stage of assembly. A test board that has already been programmed is used for this testing. The finished harness is plugged into the test board, which is then tested for errors after being configured with the necessary electrical properties.
The most current knowledge on the efficiency and recognition of cable and wire harness assemblies is taught to engineers, technicians, and makers of related products in the electronics industry through the IPC 620 certification program. It discusses how certification training can help you learn more about regulations for individual wire sealing, soldering to terminals, and many other topics.