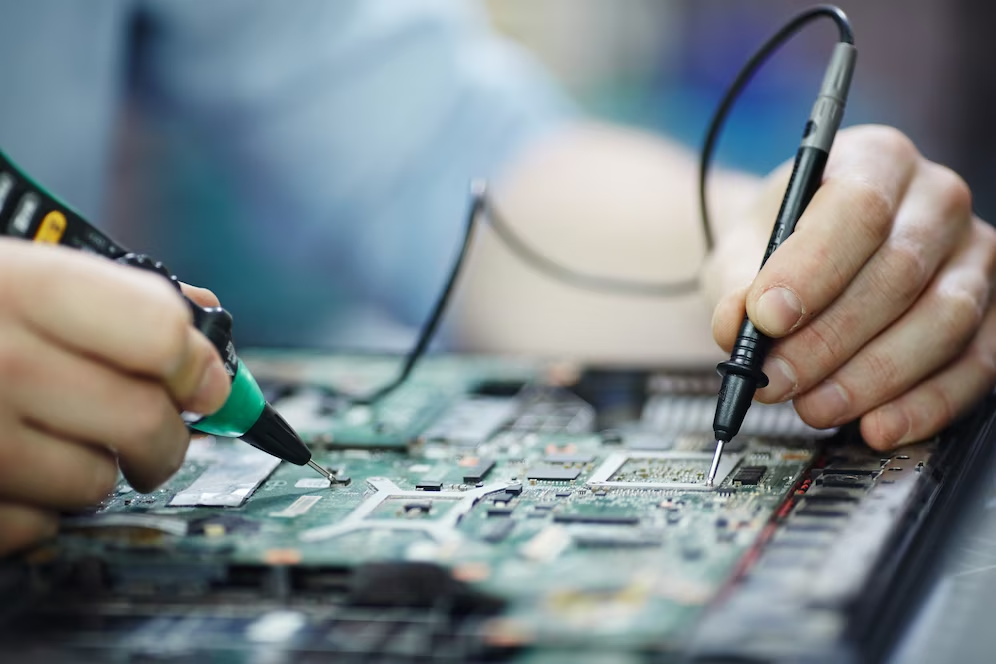
A comprehensive quality control procedure that adheres to industry standards is necessary for the production of high-quality electronic products. The IPC-A-610H is one such specification since it specifies what should be included in electronic components. However, success in electronics assembly requires more than just following the ipc-a-610h standard requirement. In this blog, we’ll discuss the IPC-A-610H standard and how it can help manufacturers go above and beyond to produce high-quality electronics.
Understanding the Purpose of IPC-A-610H
Achieving success in electronics assembly begins with grasping IPC-A-610H’s intended function. This specification offers advice on the quality of electronic components in terms of both construction and materials.
It addresses many concerns regarding electronic components, such as their design, fabrication, and testing. Your manufacturing method needs to be in sync with the specific requirements that apply to your product, so it’s crucial that you have a firm grasp of those requirements.
Establishing a Quality Management System
Implementing IPC-A-610H calls for an effective quality management system (QMS). Controlling the process, guaranteeing quality, and keeping detailed records are all essential components of this method.
A QMS that can detect and correct nonconforming products while guaranteeing that all products meet specifications is crucial. Consistent quality can be maintained, and the likelihood of defects and failures in the final product can be minimized, with the assistance of a well-implemented QMS.
Training and Certification of Personnel
IPC-A-610H mandates that anyone working on an electrical product receive training and certification. Those involved in this process range from designers and architects to assemblers and quality assurance inspectors and testers.
It is crucial to make sure that everyone on staff has received adequate training in the particular requirements of their position and is equipped with the relevant skills and knowledge to carry it out successfully.
The best way to guarantee that your staff is using the most recent standards and practices in the business is to provide them with ongoing training and certification.
Emphasizing Process Control
While the IPC-A-610H checklist is useful, process management is what really separates good from great when it comes to electronics assembly. To ensure that all goods are assembled properly and to specification, it is necessary to use work instructions, process controls, and quality checks.
A reliable process control system is essential for ensuring that all products are consistently produced and that any variations are quickly discovered and rectified.
Material Selection and Inspection
Electronic assembly materials must be inspected and chosen in accordance with IPC-A-610H requirements. As part of this process, you must check that all of your resources are in good condition and up to snuff before putting them to use.
A thorough material inspection procedure is crucial for ensuring that all inputs into a production process are of adequate quality. By placing more importance on material selection and inspection, it is possible to lessen the likelihood of defects and failures in the end product.
Design and Documentation
Electronic assembly design and documentation is essential for delivering products that satisfy specifications. Designs must be documented using standard industry tools, and then reviewed and authorized by trained professionals in accordance with IPC-A-610H.
All records must be checked for accuracy, completeness, and authenticity. This may be helpful in ensuring that all products are designed and documented to specifications and that any discrepancies are quickly discovered and corrected.
Testing and Inspection
All electronic components must undergo rigorous testing and inspection in accordance with IPC-A-610H. That covers everything from an electrical check to a visual examination to a mechanical check.
For commodities to consistently deliver on promised quality, a thorough testing and inspection procedure is essential. Putting an emphasis on testing and inspection can guarantee that all goods are of the highest quality and reliability standards.
Continuous Improvement
Excellence in electronic assembly demands a dedication to continuous refinement. In order to maintain high standards of quality and productivity, it is necessary to constantly evaluate and update the production process. A culture of continuous development is crucial for maintaining a cutting-edge production method.
Collaborating with Suppliers and Customers
Working in tandem with one’s suppliers and end-users is essential for achieving success in electronics assembly. To ensure that all materials used in production are of the necessary quality, suppliers should be held to the same standards as the manufacturer. Working together with buyers can better guarantee that the end product will satisfy their expectations.
Going Beyond Compliance
Compliance with the IPC-A-610H checklist is important, but it is not sufficient for attaining excellence in electronics assembly. This involves doing things like using established best practices and embracing a mindset of constant growth. Manufacturers who go above and beyond the required minimums see gains in quality, efficiency, and client satisfaction.
Conclusion
Manufacturers who go above and beyond the checklist and apply best practices are better able to produce electronic goods that live up to their customer’s expectations in terms of quality, durability, and functionality. Businesses that want to survive and flourish in today’s electronics industry must do more than simply meet the requirements of the IPC-A-610H standard.