Manufacturing activities are the lifeblood of many sectors, creating the goods and services that sustain economies and meet customer needs. For industrial operations to remain competitive in an era of quick technological change and global rivalry, they must keep up with the latest developments. Investing in the training and development of employees is a crucial component in attaining this. This article will discuss key training techniques that may help any manufacturing process.
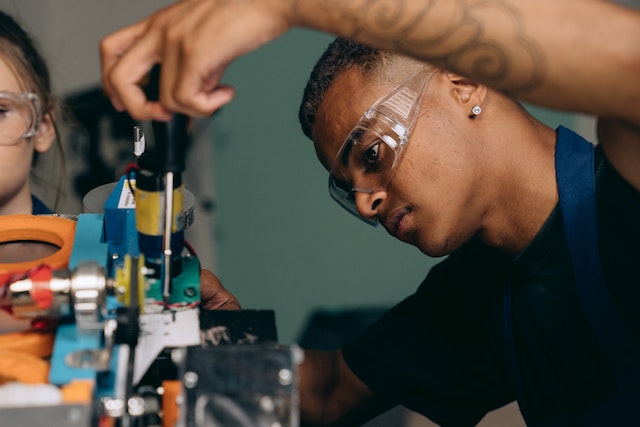
1. Lean Manufacturing Training
By putting a strong emphasis on reducing waste and improving processes, lean manufacturing concepts have transformed the industrial sector. Implementing lean methods may boost productivity, cut costs, and enhance product quality. Companies should invest in training their personnel in lean manufacturing if they want to fully realize its benefits. Employees who have received value stream mapping training can better spot waste in the production process. Thanks to this visual representation of the complete production sequence, teams can identify bottlenecks and inefficiencies. Educating staff members about 5S concepts keeps workplaces safe and structured for optimal productivity. Promoting a culture of continuous improvement by encouraging staff members to participate in Kaizen activities. These gatherings concentrate on problem-solving techniques that can significantly improve industrial procedures.
2. Training in Advanced Technology
Automation, robotics, and digital systems are some of the cutting-edge technologies widely used in modern production. To remain competitive, businesses must train their staff to use and maintain these technologies. Following are some crucial topics in technology training:
- Automation and robotics: As automation and robots are used more often in production, workers need to be trained to operate and program these systems. By ensuring that equipment is utilized to its fullest ability, this training lowers mistakes and increases productivity.
- Digital manufacturing and Industry 4.0: Employees must be skilled in data analytics, IoT (Internet of Things) sensors, and real-time monitoring systems to work in Industry 4.0, which is defined by integrating digital technology. Manufacturers may gather and evaluate data with the help of training in these areas to make wise judgments and anticipate maintenance requirements.
- Software for computer-aided design (CAD) and computer-aided manufacturing (CAM) are essential tools for the design and production processes, respectively. Employee training in these programs improves manufacturing efficiency and design correctness.
3. Safety Education
The highest concern in manufacturing processes should always be safety. Offering thorough safety training assures not only the protection of the workforce but also smooth and uninterrupted production. Important elements of safety education include OSHA compliance. In order to prevent workplace accidents and injuries, employees must get training on OSHA regulations. Employees should be knowledgeable about safety laws and recommended procedures. Employees should be trained in emergency response techniques, such as fire drills, first aid, and evacuation strategies. In dire circumstances, this information can save lives. Proper training in the safe operation of machinery and equipment is crucial to minimize the risk of accidents and injuries on the shop floor.
4. Training for Manufacturing Compliance
Legal statutes regarding product integrity are foundational in manufacturing. Comprehensive training strategies are essential to ensure compliance with these regulations. Understanding and adhering to these statutes is critical to avoiding legal issues and maintaining consumer trust. Effective training also enhances the quality and safety of manufactured products. One vital facet of this compliance is product safety and conformity representative or PSCR training. These specialized programs equip individuals with the knowledge to assess product designs, materials, and manufacturing processes, ensuring alignment with industry-specific guidelines. Moreover, it fosters a culture of accountability and responsibility, ensuring that all team members are aware of their role in upholding product integrity. By prioritizing ongoing training and education in these areas, manufacturing operations can uphold legal standards, meet customer expectations, and thrive in a competitive marketplace.
5. Development of Soft Skills
Employees in the manufacturing industry should acquire soft skills in addition to technical ones since they help foster a healthy work atmosphere and productive cooperation. Training in soft skills may enhance leadership, teamwork, and communication within industrial teams. Among the most important soft skills are:
- Teamwork: Cross-functional teams are frequently used in manufacturing processes. Training in teamwork encourages collaboration, ensuring that teams function effectively as a unit.
- Leadership and time management: Employees who have received leadership training may be more equipped to assume leadership responsibilities and participate in decision-making. Employees who receive time management training are better able to prioritize their work and fulfill deadlines.
Developing a Training Plan for Manufacturing Operations
To ensure the effectiveness of training in manufacturing operations, businesses need to develop a comprehensive training plan. A well-designed training plan outlines the objectives, content, and delivery methods for training, ensuring that employees receive the necessary skills and knowledge to excel in their roles.
Step 1: Identify Specific Training Needs
This involves conducting a thorough analysis of the skills and knowledge gaps within the workforce. By identifying areas where employees require additional training, businesses can tailor the training program to address these specific needs. This analysis can be done through employee surveys, performance evaluations, and consultation with managers and supervisors.
Step 2: Determine Training Objectives
These objectives should be specific, measurable, achievable, relevant, and time-bound (SMART). For example, the objective could be to improve machine operation skills by 20% within six months. Setting clear objectives ensures that the training program is focused and aligned with the overall goals of the manufacturing operation.
Step 3: Develop Content and Curriculum
This involves identifying the key topics and skills that need to be covered and organizing them into a logical sequence. The content should be engaging, relevant, and practical, allowing employees to apply what they have learned directly to their roles. It is important to ensure that the content is up-to-date and reflects the latest industry standards and best practices.
Step 4: Determine Delivery Methods and Required Resources
This could include a combination of classroom training, on-the-job training, e-learning platforms, and virtual reality simulations. The choice of delivery methods depends on various factors, such as the nature of the training content, the learning preferences of employees, and the available resources. It is important to select delivery methods that are engaging, interactive, and accessible to all employees.
Step 5: Evaluate Training Program Effectiveness
This involves measuring the impact of the training on employee performance, productivity, and knowledge retention. Evaluation can be done through assessments, quizzes, practical demonstrations, and feedback from employees and supervisors. By regularly evaluating the training program, businesses can make necessary adjustments and improvements to ensure its ongoing effectiveness.
Conclusion
In the present day, training is a crucial part of manufacturing processes. Manufacturing organizations must make an investment in the training of their personnel if they want to stay competitive and adapt to the quickly shifting industrial landscapes. Manufacturing operations can achieve greater efficiency, higher product quality, and a safer work environment by implementing crucial training strategies, such as continuous improvement through lean manufacturing training, advanced technology training, safety training, quality control, product safety training, and soft skills development. In the end, a skilled staff serves as the cornerstone of effective industrial operations.