In the realm of industrial production, the journey from conceptualization to the completion of a manufacturing plant is a fascinating saga of innovation, precision engineering, and meticulous planning. Among the myriad of manufacturing sectors, the lubricant industry stands out as a crucial player, ensuring smooth operations across various mechanical systems. In this article, we delve into the intricate process of establishing a Lubricant Plant Manufacturer, exploring the stages from ideation to realisation, while also spotlighting the contributions of Advance Biofuel, a leading name in sustainable energy solutions.
Ideation and Conceptualization
Every industrial endeavour begins with a spark of imagination and a vision for addressing market needs. In the case of a lubricant plant, extensive market research and analysis precede the conceptualization phase. Manufacturers identify demand trends, technological advancements, and regulatory requirements to formulate a comprehensive blueprint for the proposed facility. Factors such as production capacity, product portfolio, and sustainability objectives shape the initial concept, laying the foundation for subsequent development stages.
Design and Engineering
With the conceptual framework in place, the design and engineering phase takes centre stage. Expert engineers and designers collaborate to translate the conceptual vision into tangible blueprints, incorporating cutting-edge technologies and best practices to optimise plant efficiency and productivity. This phase involves intricate planning of equipment layout, process flow, safety protocols, and environmental considerations. Advanced simulation tools and modelling techniques are employed to anticipate operational challenges and fine-tune design parameters, ensuring seamless integration of various components within the facility.
Procurement and Construction
As design specifications are finalised, the focus shifts towards procurement and construction activities. Procurement specialists leverage global supply chains to source high-quality equipment, raw materials, and components essential for plant operations. Concurrently, skilled construction teams commence site preparation, foundation laying, and structural erection according to the prescribed timelines and standards. Rigorous quality control measures and adherence to safety protocols are paramount throughout the construction phase to mitigate risks and maintain project integrity.
Commissioning and Testing
Upon completion of construction, the newly erected facility undergoes a series of commissioning and testing procedures to validate its operational readiness. Engineers conduct comprehensive tests on equipment functionality, process efficiency, and safety systems to identify and rectify any deviations from design specifications. This phase entails rigorous performance evaluations, simulated production runs, and compliance audits to ensure regulatory compliance and adherence to industry standards. Thorough training programs are also conducted to familiarise operational staff with plant operations and maintenance protocols.
Operational Launch and Optimization
With successful commissioning, the lubricant plant is poised for operational launch, marking the culmination of months or even years of meticulous planning and execution. Initial production runs commence, and operational parameters are fine-tuned to optimise output quality, efficiency, and cost-effectiveness. Continuous monitoring and data analytics play a crucial role in identifying optimization opportunities and streamlining production processes. Feedback mechanisms are established to solicit input from stakeholders and address operational challenges proactively, fostering a culture of continuous improvement and innovation.
Innovation in Sustainable Lubricant Manufacturing
Innovation lies at the heart of sustainable lubricant manufacturing, and companies like Advance Biofuel exemplify this ethos through their pioneering approach. By harnessing the power of renewable feedstocks and advanced manufacturing technologies, they have redefined the landscape of lubricant production, offering eco-friendly alternatives to traditional petroleum-based products.
One of the key innovations driving sustainability in lubricant manufacturing is the utilisation of bio-based feedstocks. These renewable resources, such as plant oils and animal fats, serve as the foundation for bio-based lubricants that offer comparable or even superior performance to their petroleum counterparts. Advance Biofuel’s expertise in bio-refining processes enables them to extract high-quality lubricant base oils from these renewable feedstocks, minimising reliance on finite fossil fuel reserves and reducing carbon emissions.
Furthermore, advances in green chemistry have enabled the development of environmentally friendly additives and formulations that enhance the performance and longevity of bio-based lubricants. These additives not only improve lubrication efficiency but also contribute to reduced friction, wear, and corrosion, prolonging the lifespan of machinery and reducing maintenance costs. By investing in research and development, companies like Advance Biofuel continuously push the boundaries of innovation, striving to deliver lubricant solutions that meet the evolving needs of modern industry while minimising environmental impact.
Another critical aspect of sustainable lubricant manufacturing is the implementation of energy-efficient processes and resource optimization strategies. From energy-efficient equipment design to process optimization and waste heat recovery, every aspect of production is meticulously optimised to minimise energy consumption and maximise resource utilisation. Advance Biofuel’s state-of-the-art manufacturing facilities exemplify this commitment to energy efficiency, leveraging advanced automation and process control systems to minimise waste and optimise resource allocation.
Moreover, sustainable lubricant manufacturers prioritise responsible waste management practices, ensuring proper disposal or recycling of by-products and minimising environmental pollution. By adopting a circular economy approach, where waste streams are repurposed or recycled back into the production process, these companies minimise their environmental footprint and contribute to the conservation of natural resources.
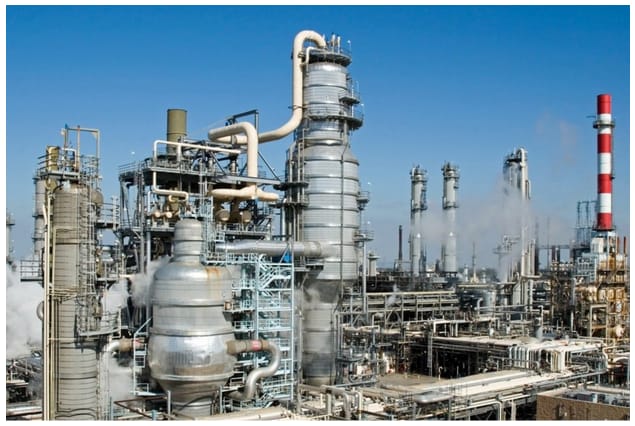
Spotlight on Advance Biofuel: Pioneering Sustainable Solutions
In the dynamic landscape of industrial manufacturing, companies like Advance Biofuel are spearheading the transition towards sustainable energy solutions. With a commitment to innovation and environmental stewardship, Advance Biofuel specialises in the production of bio-based lubricants derived from renewable feedstocks. Their cutting-edge facilities integrate state-of-the-art technologies and eco-friendly processes to deliver high-performance lubrication solutions while minimising environmental impact.
Advance Biofuel’s holistic approach to sustainability extends beyond product innovation to encompass every aspect of their operations. From energy-efficient manufacturing processes to responsible waste management practices, they prioritise resource conservation and carbon footprint reduction. By leveraging bio-based alternatives to traditional petroleum-based lubricants, Advance Biofuel contributes to a greener, more sustainable future for the industry and the planet.
Conclusion
The journey from concept to completion of a lubricant plant exemplifies the intricate interplay of vision, expertise, and innovation inherent in industrial manufacturing. Each stage of the process, from ideation and design to commissioning and optimization, requires meticulous planning and execution to ensure the success of the endeavour. Companies like Advance Biofuel epitomise this ethos, driving industry evolution towards sustainability and efficiency through their relentless pursuit of excellence. As the demand for lubricants continues to grow in tandem with industrial progress, the journey from concept to completion remains a testament to human ingenuity and the pursuit of excellence in engineering and manufacturing.
Thanks for making complex ideas easy to understand.
To save money and energy both, we would suggest you get solar solutions for your industry. Thank you.
3D Product Modeling and Rendering Service
Supercharge your product visuals with our 3D Product Rendering Services Bring your ideas to life Get a free demo and enhance your brand s appeal!Cutting Edger