Creating a new product in today’s rapidly changing industrial environment requires a systematic approach to maximizing the likelihood of that product’s commercial success. Bringing an idea into reality includes working through several critical processes during product development, each of which must be completed in detail. Each stage, beginning with the generation of an idea and continuing through the manufacturing process, demands meticulous planning, strategic decision-making, and collaborative effort across numerous teams. This article will highlight the significant stages involved in creating a product for production, as well as go deeper into the complexities of each stage.
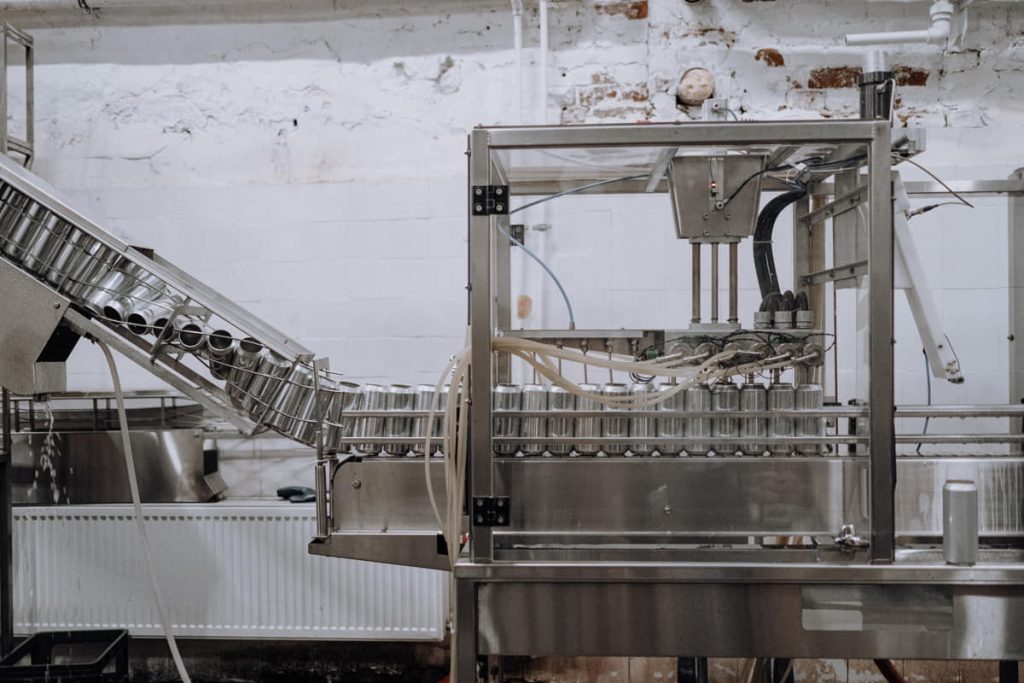
Exploring Potential Customers and Generating Ideas
Conducting in-depth market research before beginning the product development process is necessary. Businesses must understand their target demographic, conduct thorough analyses of their competitors, and locate unfilled niches in the market. This research will serve as a basis for creativity, which is the process of coming up with ideas to answer the needs discovered in the market. The development of novel ideas can be aided by a variety of methods, including but not limited to focus groups, customer surveys, and brainstorming sessions.
Develop And Validate The Concept
After a list of potential ideas has been compiled, the following step is to develop and verify each notion. This entails developing the initial thoughts into workable concepts and carrying out investigations to see whether or not the endeavor is even possible. The viability and potential of the product are evaluated through the creation of prototypes and mock-ups. The input and feedback of stakeholders, such as customers and industry experts, are crucial in further refining and validating the concepts.
Detailing The Design And Engineering Work
Now that we have concepts proven to work, it is time to move on to the full design and engineering stages. During this stage, you will translate the idea for the product into detailed technical specifications and designs. Design engineers collaborate closely with the team responsible for product development to produce three-dimensional models, run simulations, and iteratively improve the design. It is necessary to pay close attention to the details and be precise to guarantee that the product can be manufactured, perform properly, and last for a long time.
Select The Materials And Vendors
One of the most important steps in production is selecting the appropriate materials and suppliers. The materials that are used can have a considerable influence on the quality, pricing, and performance of the product. Selecting materials that match the product’s criteria while also considering issues such as availability, pricing, and environmental sustainability requires a significant amount of research and evaluation. Similarly, achieving success in manufacturing requires locating trusted suppliers that can continuously produce high-quality components.
The Development And Testing Of Prototypes
Creating a prototype is an essential step in developing a new product because it enables businesses to test and verify the design, functionality, and performance of their product before moving on to mass production. After the creation of physical prototypes, they are put through a battery of tests that include durability and stress simulations and evaluations of how users interact with the product. In both the product development and production processes, aluminum prototype tools provide several benefits.
These instruments offer a dependable and practical method for creating prototypes because of their low prices, fast lead times, lightweight structure, and better cooling efficiency. Prototype tools are a popular choice among producers who want to streamline the processes of product development and testing because of their versatility and compatibility with other tools and materials. The insights gathered through testing helped uncover any design defects or performance difficulties that needed to be resolved before the manufacturing process could begin.
Planning The Manufacturing Process
When the final design and the working prototype have been given the green light, it is time to begin planning the manufacturing process. During this process stage, you will establish a production plan, determine the production methods that will yield the highest efficiency level, and set up quality control systems. During this stage of the process, manufacturers need to consider various aspects, including production volume, required equipment, labor costs, and supply chain logistics. Design engineers, production managers, and suppliers must work together to maximize the efficiency of the manufacturing process.
Manufacturing And Putting Together
It is possible to begin production and assembly now that the manufacturing process has been thought out and the appropriate tools and equipment have been acquired. During this stage, the product’s individual components will be physically crafted before being put together to form the finished good. Maintaining stringent quality control throughout the production process is necessary to guarantee that every item satisfies the requirements that have been outlined. To get reliable and high-quality results constantly, it is essential to do routine checks and tests and stick to established protocols.
Testing And Quality Control
The process of quality assurance is an ongoing one that occurs throughout all stages of product development as well as manufacturing. During this stage, the product is subjected to exhaustive testing and inspections to establish whether or not it satisfies the prerequisite criteria and requirements. Testing of the product’s functioning, durability, and conformity with regulatory standards are subjected to various examinations. These examinations include performance, reliability, and safety testing, among others. To ensure that the quality of the product is not compromised, fast action is taken to resolve any problems or faults that are discovered.
Conclusion
In conclusion, developing a product for production is exhaustive and iterative, involving various essential phases. Each stage adds to the overall success of a product, from initial market research and creativity to market launch and beyond. Companies can design goods that satisfy the needs of their customers, conform to the norms of their industry, and stand out in the market if they adhere to a defined methodology and include their customers’ feedback throughout the process. Not only does efficient product development guarantee that the manufacturing process will go smoothly, but it also maximizes the product’s potential for commercial success.