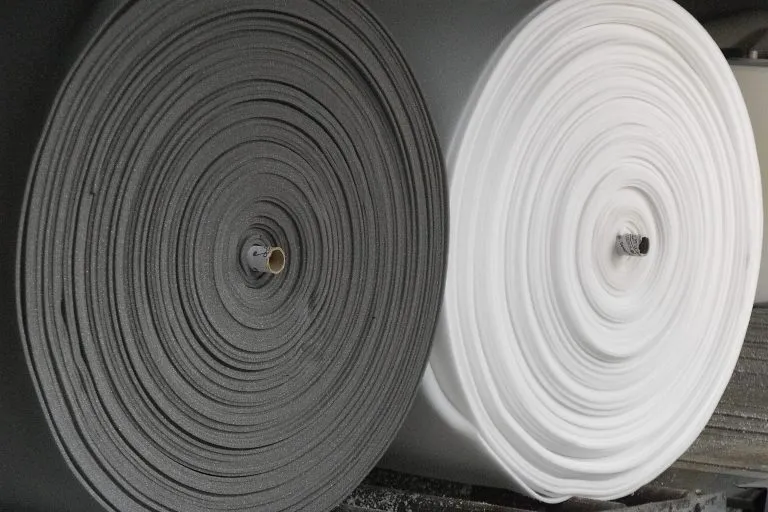
High-density polyurethane foam, commonly known as high-density PU foam, represents a significant advancement in materials science. This specialised polymer form stands out for its exceptional strength-to-weight ratio, remarkable durability, and versatile application potential. Its density, typically ranging from 45 to 65 kilograms per cubic meter, is the fundamental characteristic that sets it apart, which contributes to its superior performance across various applications.
The Manufacturing Process
The production of high density PU foam involves a sophisticated chemical reaction between polyols and isocyanates. This process, known as polymerization, requires precise control over temperature, pressure, and catalyst concentrations. During manufacturing, specialised equipment combines these components under carefully monitored conditions, initiating an exothermic reaction that creates the foam’s characteristic cellular structure.
The cellular architecture of high density PU foam is crucial to its performance. Advanced manufacturing techniques allow for creating both open-cell and closed-cell variations, each serving specific purposes. The controlled expansion process determines the final density, with higher densities achieved through specialised formulations and precise process control.
Quality Control and Testing
Quality assurance in high density PU foam production involves rigorous testing protocols. Key parameters include density measurement, compression set testing, tensile strength evaluation, and elongation assessment. These tests ensure the foam meets industry standards and application-specific requirements. Environmental chambers simulate various conditions to verify performance under different temperatures and humidity levels.
Properties and Characteristics
High-density PU foam exhibits several distinctive properties that make it invaluable across industries. Its exceptional compression resistance allows it to maintain shape under sustained pressure, while its resilience enables quick recovery after deformation. The material demonstrates excellent thermal insulation properties and remarkable sound absorption capabilities.
The foam’s closed-cell structure provides inherent moisture resistance, making it suitable for applications in humid environments. Its chemical stability ensures long-term performance without degradation, and its fire-retardant properties can be enhanced through specific additives during manufacturing.
Industrial Applications
The automotive industry extensively utilises high density PU foam in seating systems, interior components, and structural elements. The material’s ability to absorb impact energy while maintaining shape makes it ideal for safety applications. In construction, high-density PU foam is thermal insulation, structural support, and sound-dampening material.
Marine applications benefit from the foam’s water resistance and durability, using it in flotation devices and composite structures. The aerospace industry incorporates interior panels and seating systems material, taking advantage of its lightweight nature and fire-resistant properties.
Commercial and Residential Uses
High-density PU foam revolutionises seating comfort and durability in the furniture industry. The material’s consistent support characteristics and long-term resilience make it ideal for mattresses, sofas, and chairs. Its adaptability allows for various firmness levels, meeting diverse comfort preferences.
Packaging employs high-density PU foam to protect sensitive equipment during transport. Its shock-absorbing properties and customisable shapes provide superior protection for electronic devices, medical equipment, and fragile items.
Sustainability and Environmental Considerations
Modern manufacturing processes focus on environmental sustainability through reduced emissions and energy consumption. Recycling programs now enable the processing used foam into new products, contributing to circular economy initiatives. Developing bio-based polyols offers more sustainable raw material options, reducing dependency on petroleum-based resources.
Cost Analysis and Economic Benefits
While initial material costs exceed those of standard foams, the long-term economic benefits justify the investment. Extended product lifespan, reduced maintenance requirements, and lower replacement frequency contribute to overall cost efficiency. The material’s versatility often simplifies manufacturing processes, saving production costs.
Future Developments and Innovations
Research continues to develop enhanced properties through novel chemical formulations and manufacturing techniques. Emerging trends include integrating smart materials, improved fire resistance, and enhanced biodegradability. These innovations aim to expand applications while addressing environmental concerns.
Installation and Maintenance
Proper installation techniques ensure optimal performance across applications. The material requires specific handling procedures during cutting, shaping, and bonding. Regular maintenance typically involves simple cleaning protocols, with minimal special care requirements for most applications.
Safety Considerations
Safety protocols in manufacturing and installation focus on proper ventilation and personal protective equipment. Modern formulations comply with strict safety standards regarding chemical emissions and fire safety. Proper storage and handling guidelines ensure long-term stability and performance.
Selection Guidelines
Choosing the appropriate high density PU foam specification involves considering multiple factors, including application requirements, environmental conditions, and performance expectations. Understanding load requirements, exposure conditions, and regulatory compliance needs guides proper material selection.
Market Outlook
The global high density PU foam market continues to expand, driven by increasing demand across industries. Growth trends indicate rising adoption in emerging markets and new applications. Technological advancements and environmental regulations shape market development and innovation directions.
Conclusion
High-density PU foam represents a crucial material in modern manufacturing and construction. Its versatility, performance characteristics, and evolving sustainability profile position it as a key component across numerous applications. Understanding this valuable material’s properties, manufacturing processes, and application potential enables optimal utilisation. As technology advances and environmental consciousness grows, high-density PU foam continues to adapt and improve, meeting the changing needs of industries and consumers alike.