When you think of copper, what comes to your mind? Whether it is at your home or at work, you will notice that most of the wires are made of copper, because copper is an excellent conductor of electricity. It is understandable why copper plating is a great choice on metal surfaces which require a high level of conductivity. Copper is rather a dull reddish-brown color. But if a more attractive finish is desired, the finish can be brightened with the use of additives. In recent times copper seems to be ‘covering up’ many industrial sectors.
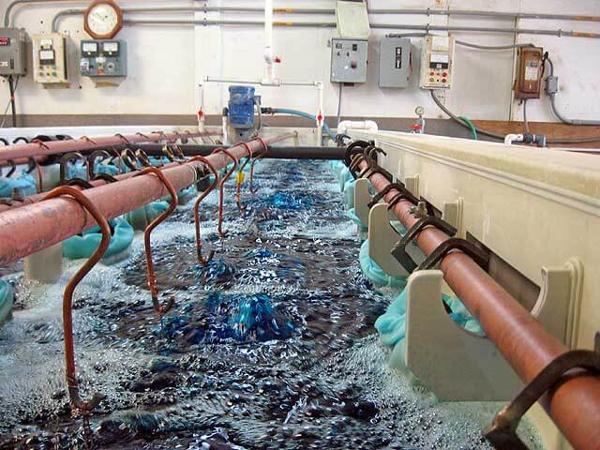
In situations where enhanced adhesion for additional coatings of other materials is required, copper plating is used as an undercoat because it provides smooth and uniform coverage. The Copper electroplating solution can be used as a treatment in preparation of surfaces for soldering. Also, it is common for aerospace and electronics industries to apply copper plating on plastic components.
COPPER PLATING
The process of plating one metal over another is called electroplating. Copper plating is done for various purposes, most commonly it is done to impart corrosion resistance and for decorative purposes. Copper electroplating is at times used for masking as a heat treat stop-off because when needed it allows for selective heat-treating. Additionally, copper electroplating may be used in a variety of plating applications where greater thickness build and high electrical conductivity are required. As exemplified by copper plating on plastic, copper plating is sometimes used for the metallization of non-metallic materials and in electroforming. It is also used for printed circuits through hole plating and with semiconductors.
Copper Plating for Industrial Use
Copper plating is used more extensively in many industries more than we may know. This resourceful metal product can withstand various environments where other metal products may not be appropriate or will not offer the needed characteristics for a positive result. Discussed here below are just a few industries that use copper plating and the reasons why copper plating is gaining significance in those industrial sectors:
Copper offers many benefits, with regard to electroplating. Copper is a soft and malleable metal. Therefore it is an excellent choice for electroplating with other flexible metal objects or materials. For example, Copper plating is perfect for marine use. Copper has inherent antifouling properties. This would mean that it can be used for parts such as propeller shafts and boat hulls. Since organisms and bacteria react to the innate characteristics of copper, the use of copper plating in marine work reduces mechanical breakdowns and saves cleaning time.
Even when the object is bent, copper will not separate from other metals. The major reason why copper electroplating is widely used in the electronics industry is because copper has excellent conductive properties making it more effective than other materials for use with an electrical component. When used as a base coat for nickel steel plating, in comparison to other materials electroplated, copper is able to provide superior protection against corrosion.
For example, there is a wide variety of use in the HVAC industry for copper plating. From boilers to tanks and steam condensers to heat exchangers everything can be made from copper plate. The advantage is that copper has high thermal conductivity, and so it is ideal for the needs of the cooling and heating industry.
COPPER ELECTROPLATING SOLUTIONS
While copper is an extremely effective electroplating solution in many situations, a few specific properties of copper bring in certain limitations in its use. Since copper is a highly active metal, it is not always the best option for direct plating with iron unless nickel is initially applied as a base coat.
Also, to ensure maximum adhesiveness, it might be essential to use a cyanide solution in conjunction with the copper electroplating solution. One needs to exercise a great amount of caution during the copper plating process because of the highly toxic nature of cyanide. Since copper is somewhat dull in color, additives may be needed for a brighter finish. In order to ensure a highly functional finished product, there are several essential steps in the copper electroplating process. Items to consider when placing an order for copper plating include sampling and test procedures, coating requirements and final rejection, rehearing or certification.
Conclusion
Copper has become the preferred plating option for the electronics and semiconductor industries. The characteristics of copper have added to the significant usage of copper plating in the industrial sector.
You got my attention when you said that the plating process is done for various purposes. As you said, it is done to impart corrosion resistance. This reminded me of industrial companies that deal with medical devices and other important equipment. I could imagine how electroplating metal finishing could ensure quality services.
It really stood out to me when you mentioned that copper plating is commonly found in many industrial settings. I would guess copper is popular because of how abundant it is. Since copper is so abundant, it probably is much more affordable.