No business ever intends to sabotage its employees, but accidents can always happen. There is no reason to create conditions for the same by deploying forklifts without lights. Forklifts are the compact trucks that transport and load various kinds of materials in warehouses and other work spaces. Even as the trucks operate in their designated areas, they need to use lights to indicate their presence.
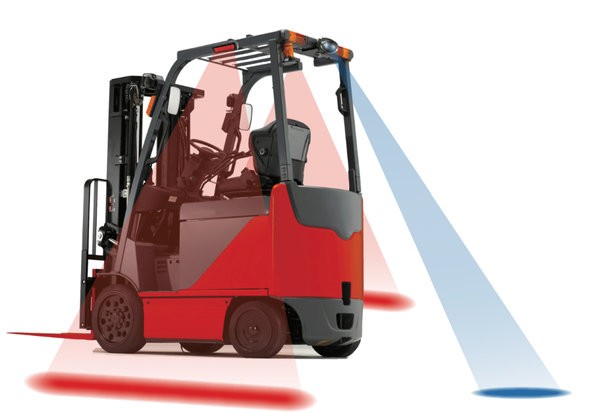
In case a truck has been extensively used, there are chances that its lights may have been damaged. If the above statement is true, a company may have to buy forklift blue light. It makes sense to buy more than one light from a reputed vendor for maintaining inventory. For this, purchase department employees must be willing to spend time searching for suitable vendors.
Forklift trucks have forked platforms attached to them. These platforms are raised or lowered to stack goods. Many workers have been found to be using earphones or headphones in the work area, and for them to know how far the machines are, there must be warning lights. Also, these lights are suitable not just to move in front but to reverse as well. They can be mounted on the machine with minimum of efforts.
Buy lights at attractive prices
Any businessman or company will try to search for maximum value in a deal, and the same holds true with parts such as forklift lights as well. Again, purchase department professionals have to talk to a number of vendors and try to get the best prices for their companies. Of course, this does not mean that they will disregard quality, but will simply strike a balance between the two.
Do not drill holes into forklifts
A lot of forklift users and their repair mechanics have been seen trying to drill holes into truck arms or walls for attaching external accessories. This is not a healthy practice as it can have an adverse affect of the vehicle’s structural strength. The practice is also discouraged as per OSHA (Occupational Safety Hazards and Attachments) in the USA. If individuals still persist with such activities, it may result and accidents as well as major damages.
There are a number of modifications that can be done, but they require prior approval from OSHA. These include:
- Swapping the counterweights
- Modifications which affect the visibility
- Changing attachments such as masts, types of tires, and forks
- Cutting or drilling into the hood
Different parts of forklifts
It is important to make sure that the forklift operator is making appropriate use of the forklift truck. For this purpose, he must be trained on identifying and knowing about parts of this vehicle. These parts are as follows:
- Blue or red blue warning lights
- Forks
- Carriage
- Mast
- Cab
- Power supply
- Overhead guard
- Counterweight
- Tires
- Tilt cylinder
- Load backrest
- Hydraulic lift cylinder
Always choose well known vendors for parts
Operations can continue without unnecessary obstructions when companies buy warning lights and other forklift parts from reputed vendors in this field. This fact holds true for both new forklifts as well as replacement parts. Logistics employees cannot devote much time away from their businesses to follow up on vendors. Such involvement may even lead to major operational delays.
Illuminate all areas
Forklift warning lights make pedestrians and employees aware of the truck’s presence even in dimly lit areas. This is highly useful in various corners of large warehouses where the lighting may be inadequate in certain areas. Suitable quality of parts will ensure maximum safety and also help enhance employee morale.
Reducing accidents due to forklifts
Forklifts are always in motion, and are also very important for continuous commerce. Material handling must be undertaken only with a safety protocol in place. Roughly 100,000 accidents take place every year in areas around forklifts. Fortunately, there are a number of methods and tools that can ensure a safe environment. These are as follows:
- Training the forklift operator– It is necessary to have a proper safety policy and training to avoid several potential accidents. The operators have to understand that forklifts are quite different from cars in terms of technologies. They have to be taught fundamentals of operation in class, along with maintenance, proper ways of getting on to the forklifts, and maintenance. Operators get practical chances to use forklifts after training, as per OSHA.
- Proper workspace design and layout– Design must be as per the frequency of material flow and its volume. Poorly designed material flow is likely to lead to accidents. The design also must keep in mind the truck’s design, as forklifts are not designed to operate in all environments.
- Maintenance- Before the start of every shift, operators must inspect their forklifts carefully. He should be in possession of a comprehensive checklist for this purpose. However, there may be challenges in case multiple drivers use it in a day.