Solenoid valves are indispensable components in various industries, playing a crucial role in controlling the flow of liquids and gases. From industrial automation to medical equipment, solenoid valves provide precise and reliable operation, making them an essential part of modern technology.
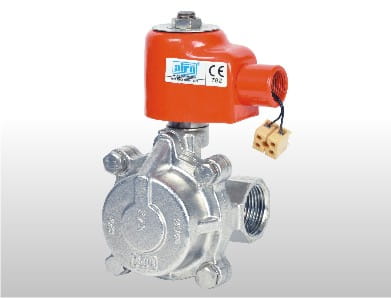
What are solenoid valves?
Solenoid valves are electromechanical devices used to control the flow of fluids through a system. They consist of a coil of wire wrapped around a hollow core, known as a solenoid, which generates a magnetic field when an electric current passes through it. This magnetic field activates a plunger or a piston, allowing or blocking the flow of fluid through the valve.
Importance of solenoid valves in various industries
A solenoid valve finds widespread use in industries such as manufacturing, automotive, aerospace, and healthcare. They are employed in applications ranging from controlling the flow of water and air in HVAC systems to regulating the flow of fuel and chemicals in industrial processes. Their ability to provide precise and instantaneous control makes them indispensable in ensuring the efficient operation of complex systems.
Working Principle of Solenoid Valves
Solenoid valves operate on the principle of electromagnetism. When an electric current is applied to the coil of the solenoid, it generates a magnetic field, which exerts a force on the plunger or piston inside the valve. This force moves the plunger or piston, opening or closing the valve and allowing or blocking the flow of fluid.
Types of Solenoid Valves
There are several types of solenoid valves, each designed for specific applications and operating conditions.
Direct-acting solenoid valves
Direct-acting solenoid valves operate by using the magnetic force generated by the solenoid to directly lift the plunger or piston, opening or closing the valve.
Pilot-operated solenoid valves
Pilot-operated solenoid valves use a smaller solenoid to control the flow of fluid to a larger piston or diaphragm, allowing for greater flow rates and higher pressure capabilities.
Two-way and three-way solenoid valves
Two-way solenoid valves have two ports—one for the inlet and one for the outlet—and are used to either allow or block the flow of fluid. Three-way solenoid valves have three ports and are used to divert the flow of fluid between two different paths.
Normally open and normally closed solenoid valves
Normally open solenoid valves allow fluid to flow through the valve when de-energized, while normally closed solenoid valves block the flow of fluid when de-energized.
Applications of Solenoid Valves
Solenoid valves are used in various applications across various industries due to their versatility and reliability.
Industrial automation
In industrial automation systems, solenoid valves are used to control the flow of air, water, and other fluids in pneumatic and hydraulic systems.
HVAC systems
Solenoid valves play a critical role in HVAC (heating, ventilation, and air conditioning) systems, where they regulate the flow of refrigerant and control the operation of heating and cooling components.
Medical equipment
In medical devices such as infusion pumps, anesthesia machines, and diagnostic equipment, solenoid valves are used to precisely control the flow of fluids and gases.
Automotive industry
Solenoid valves are used in automotive applications such as fuel injection systems, transmission control, and emission control systems, where they help optimize engine performance and efficiency.
Factors to Consider When Choosing Solenoid Valves
When selecting solenoid valves for a specific application, several factors must be taken into account to ensure optimal performance and reliability.
Fluid compatibility
It is essential to choose a solenoid valve that is compatible with the type of fluid being controlled, taking into account factors such as chemical composition, viscosity, and temperature.
Pressure and temperature requirements
The operating pressure and temperature of the system must be considered when selecting a solenoid valve to ensure that it can withstand the conditions without failure or leakage.
Size and port configuration
Solenoid valves come in a variety of sizes and port configurations, so it is crucial to choose one that matches the flow rate and connection requirements of the system.
Voltage and electrical connections
The voltage and electrical connections required to power the solenoid valve must be compatible with the available power source and control system.
Installation and Maintenance of Solenoid Valves
Proper installation and maintenance practices are essential to ensure the reliable operation of solenoid valves and prevent premature failure.
Proper installation procedures
Solenoid valves should be installed according to the manufacturer’s recommendations, taking into account factors such as orientation, mounting position, and sealing requirements.
Regular maintenance practices
Routine maintenance, such as cleaning, lubrication, and inspection of components, should be performed to keep solenoid valves in optimal condition and prevent malfunctions or leaks.
Troubleshooting common issues
Identifying and troubleshooting common problems with solenoid valves, such as coil burnout, clogging, or leakage, can help minimize downtime and repair costs.
Advantages of Solenoid Valves
Solenoid valves offer several advantages over other valves, making them the preferred choice in many applications.
Fast response time
Solenoid valves can open and close almost instantaneously when energized, allowing for precise control of fluid flow and rapid response to changes in system conditions.
Energy efficiency
Solenoid valves consume minimal power when in the open or closed position, making them highly energy-efficient compared to other types of valves that require continuous power to maintain their position.
Compact design
Solenoid valves are compact and lightweight, making them easy to install and integrate into existing systems with limited space.
Versatility in applications
Solenoid valves are available in a wide range of sizes, materials, and configurations, making them suitable for a variety of fluid control applications across different industries.
Limitations of Solenoid Valves
Despite their many advantages, solenoid valves also have some limitations that must be considered when selecting and using them in a system.
Limited pressure and temperature range
Solenoid valves may not be suitable for high-pressure or high-temperature applications, as they can experience performance issues or failure under extreme conditions.
Sensitivity to contaminants
Solenoid valves can be sensitive to contaminants such as dirt, debris, or corrosive substances, which can cause clogging, leakage, or premature wear of components.
Potential for coil burnout
Continuous or frequent energization of the solenoid coil can lead to overheating and burnout, reducing the lifespan of the valve and requiring replacement.
Conclusion
Solenoid valves are essential components in a wide range of industries, providing precise and reliable control of fluid flow in various applications. Understanding their working principle, types, applications, and limitations is crucial for selecting the right valve for a specific system and ensuring its optimal performance and longevity.