Specific Laser Sintering (SLS) has turned out to be a standout amongst the most generally utilized advancements for producing added substance. Today, its a long away from being an apparatus utilized exclusively for making models. SLS innovation has turned into suitable methods for delivering low-volume end parts and bolster parts, similar to dances and installations, over a scope of businesses. With the advantages of SLS prototypes innovation being complex, the innovation has opened up new conceivable outcomes for engineering and design.
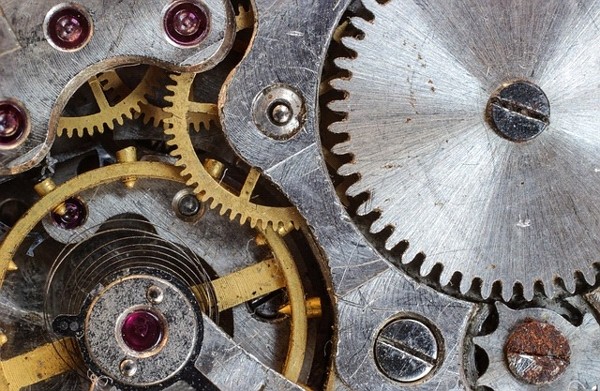
Now let us understand that why it is a good idea to think about the production of SLS printed parts?
Make profoundly intricate, lightweight components:
SLS innovation is perfect for making profoundly complex parts since it doesn’t need help structures. It is in contrast to SLA (stereolithography) and FDM (Intertwined Statement Displaying). Unsintered powder left over from the printing procedure is utilized to give extra quality and backing to the part, in this way going about as its structure for support.
Time can be saved and production can be boosted:
SLS enables you to print complex geometries in a solitary print run that would customarily require various parts to deliver. This implies various parts are easy to be printed immediately. It helps in saving time and exertion while additionally boosting space building. Parts can even be included while printing is in advancement. It thereby permits both further replications of the part and structure changes in the last minute to be included. It is better than restarting the whole process of production from the beginning.
Production of substantial modified and on-request parts:
The likelihood of utilizing SLS innovation is to make items “on demand”. It can likewise fundamentally diminish the expenses of keeping up a broad stock of parts as segments and items can be fabricated at the purpose of need. One case of this is carrier Emirates, who a year ago uncovered its reception of SLS innovation to print parts for its aircraft lodges.
Shorter Item Improvement Cycles:
SLS empowers the fast creation and testing of models over a time of a few days, consequently lessening the generation improvement cycle. Moreover, end parts can be made with no requirement for costly tooling, as is required for customary ways for manufacturing.
Solid Material Properties:
The most regularly utilized materials for SLS are polyamides, designing thermoplastics with mechanical properties perfect for a scope of useful applications. With isotropic properties and synthetic and warmth opposition, parts made with SLS innovation rival those delivered through customary assembling strategies, for example, injection molding.
Conclusion:
SLS prototype innovation surely gives a scope of advantages to mechanical applications. In any case, before choosing to incorporate SLS into your in-house production forms, it would, in any case, be reasonable to initially consider your printing needs. It is because putting resources into an SLS machine is a matter of investing huge amounts. All things considered, one key component of effectively utilizing 3D printing innovation is guaranteeing that you coordinate your necessities to the innovation that you are adopting.