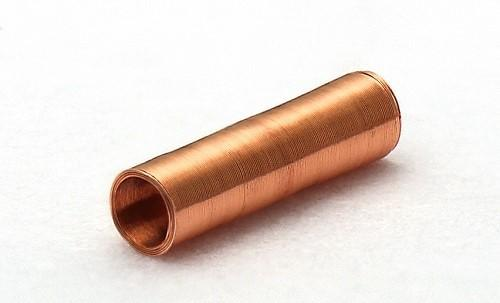
In the vast world of electronics, a delicate technique called micro-soldering reigns supreme. With its ability to join tiny components onto circuit boards, micro soldering plays a pivotal role in various industries, from aerospace to medical devices. In this blog, we will explore the intricacies of the micro-soldering process, its applications, and the invaluable contributions it makes to the realm of precision electronics.
I. Understanding Micro Soldering
A. Definition and Significance
Defining micro soldering as the precise process of soldering tiny electronic components
Highlighting the importance of micro soldering in ensuring the functionality and reliability of complex electronic devices
B. Applications of Micro Soldering
Aerospace and Defense: Micro soldering is crucial for manufacturing and repairing mission-critical avionics and defense systems.
Medical Devices: From pacemakers to medical imaging devices, micro soldering enables the creation of life-saving technologies.
Consumer Electronics: Mobile phones, tablets, and wearable devices heavily rely on micro-soldering for compact and efficient designs.
II. Tools and Equipment for Micro Soldering
A. Micro Soldering Irons
Specialized soldering irons with fine tips and temperature control to handle small-scale components
Different types of micro soldering irons, such as pencil irons, tweezers, hot air rework stations, and hot plates
B. Solder and Flux
Choosing the right solder wire diameter and composition based on the specific soldering requirements
The significance of flux in facilitating proper solder flow and ensuring reliable joints
C. Microscopes or Magnification Systems
The importance of magnification for precise visual inspection and accurate soldering
Options for magnification, including microscopes, magnifying glasses, or loupes
III. The Micro Soldering Process
A. Preparation
Setting up a clean and organized workspace for optimal visibility and accessibility
Gathering the necessary tools, components, and safety equipment
B. Component Removal and Replacement
1. Component Removal
– Employing desoldering techniques such as hot air rework, solder wick, or desoldering braid
– Exercising caution to avoid damaging neighboring components.
2. Component Replacement
– Ensuring precise alignment and positioning of the new component
– Applying the right amount of heat and solder to form reliable and durable joints
C. Soldering Techniques and Tips
Pre-tinning the soldering iron tip for improved heat transfer and solder flow
Implementing thorough solder joint inspection and quality control measures
Avoiding common pitfalls, such as overheating, solder bridges, and cold joints.
IV. Expanding the Horizon: Challenges and Best Practices
A. Handling Small-Scale Components
Tips for delicate component handling to minimize the risk of damage
Utilizing specialized tweezers and vacuum pens for precise placement
B. Effective Heat Management
Maintaining optimal heat control to prevent overheating and component damage
Implementing heat sinks and thermal insulation techniques for sensitive components
C. Cultivating Expertise Through Practice
Enhancing micro-soldering skills through dedicated practice and experimentation
Nurturing patience and composure when engaging in intricate tasks.
Conclusion:
Micro soldering represents the pinnacle of precision electronics, enabling the creation, repair, and modification of intricate circuitry. From critical aerospace systems to life-saving medical devices and cutting-edge consumer electronics, the art of micro-soldering contributes to technological advancements and innovation. By understanding the process, acquiring the right tools