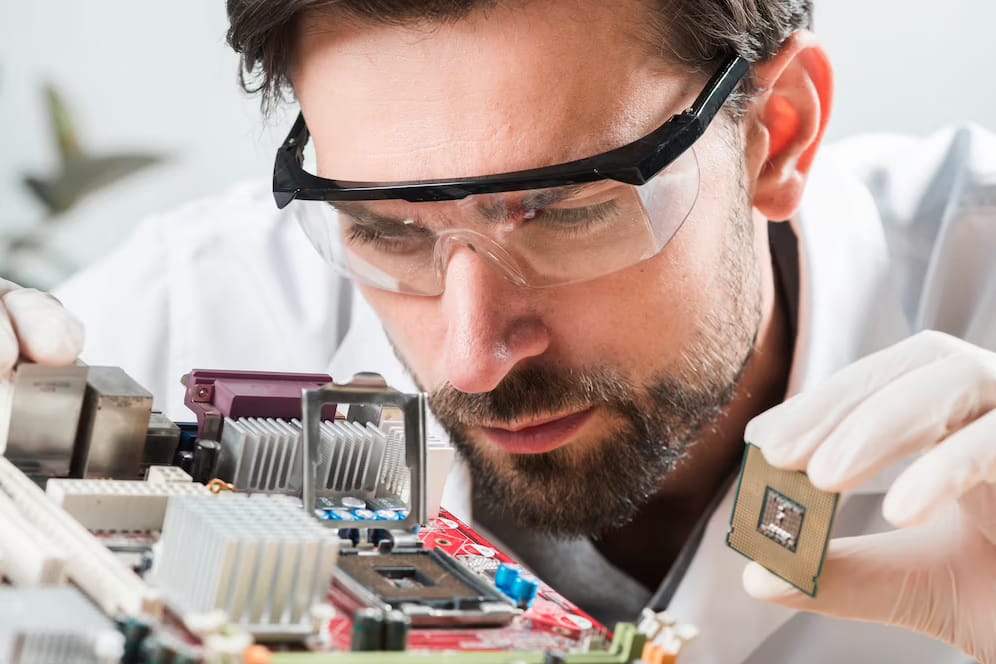
Reworking circuit boards are an integral part of the manufacturing procedure for electronic components. This procedure involves the removal and replacement of individual electronic components on a printed circuit board. While there are several methods for fixing circuit boards, analyzing the Ball Grid Array (BGA) components is crucial. The BGA inspection methods are heavily used in the circuit board rework process. Here are some new methods for inspecting BGAs that can save you time and effort:
- X-Ray Inspection
Electromagnetic radiation is used in non-destructive testing methods like X-ray inspection to view the PCB’s inside components. This technique is commonly used in BGA inspection, and it allows for the detection of cracks, voids, and cold solder junctions that would otherwise go undetected.
By passing an X-ray beam through a BGA part, the solder joints may be examined. This image analysis can be used to spot flaws. Since X-ray inspection can reveal issues with components that are otherwise hidden, it is indispensable for BGA inspection.
- Optical Inspection
When performing an optical evaluation, a microscope is used to check the PCB’s surface for defects. This technique of testing is able to spot surface faults including cracks, chips, and scratches by magnifying the PCB.
Visual defects are easy to miss, but an optical inspection will uncover them during BGA inspection. This technique allows the solder joints of a BGA component to be inspected for flaws by looking at the component’s borders.
- Automated Optical Inspection (AOI)
Automated Optical Inspection (AOI) is one technique that uses machines to inspect the PCB for defects. Using algorithms, this technique compares the captured PCB image with the expected image and flags any inconsistencies.
As it can detect issues like component misalignment, component absence, and solder bridges, AOI is a necessary BGA inspection technique. Compared to manual optical inspection, this technology is both faster and more precise, and it can uncover defects that aren’t always visible to the naked eye.
- Infrared Inspection
Infrared inspection uses thermal radiation to detect malfunctions on a PCB. Problems such as overheated components, cold solder connections, and temperature gradients can be identified using this testing procedure.
After warming the PCB using a heat source, the board’s thermal profile can be captured with an infrared camera for an in-depth analysis. This image analysis can be used to spot flaws. If there are problems with the PCB’s thermal qualities, they can only be found by infrared inspection, which is why it’s so important for BGAs.
- CT (Computed Tomography) Scan
The PCB can be viewed in three dimensions with the use of X-rays via advanced inspection techniques like CT scanning. This technique is commonly used to inspect BGAs for defects such as voids, fractures, and misalignments.
A 3D representation of the PCB is reconstructed using computational techniques based on a series of X-ray images obtained from a variety of angles. CT scanning is an important BGA inspection method since it provides a complete picture of the PCB’s internal structure.
- XRF (X-Ray Fluorescence) Inspection
Solder balls may contain contaminants that compromise solder joint quality, which can be uncovered by X-ray fluorescence (XRF) inspection. The atoms in the solder balls are excited by the X-ray beam, causing them to emit X-rays at a certain wavelength. A detector picks up the emitted X-rays, and the solder balls’ elements are identified using spectral analysis. Before a BGA component is soldered to a printed circuit board, an X-ray fluorescence (XRF) inspection is performed to ensure the solder balls are of sufficient quality.
- C-SAM (C-Mode Scanning Acoustic Microscopy) Inspection
The C-SAM process involves sending high-frequency sound waves into the BGA component through a transducer. These waves penetrate the BGA part and are reflected by structures therein. The transducer picks up the echoes and uses them to recreate the BGA part’s inner workings.
C-SAM inspection can find flaws in the BGA component like delamination, cracks, and voids. The quality and dependability of the BGA component can be guaranteed by completing this examination during production.
- SEM (Scanning Electron Microscopy) Inspection
Using a high-energy electron beam, SEM inspection is an advanced technique for examining the inner workings of a BGA component. As it can reveal the root of the failure in great detail, the method excels at failure analysis.
The BGA part is initially broken apart using a focused ion beam for SEM inspection. The parts are then scanned using a high-energy electron beam inside a vacuum chamber.
Secondary electrons, backscattered electrons, and X-rays are emitted as a result of the electrons’ interactions with the sample’s atoms. Detectors pick up on these signals and utilize them to build up an image of the BGA part’s inner workings.
Conclusion
This increasing complexity of electronic gadgets calls for more sophisticated BGA inspection techniques than ever before. Using these strategies in circuit board repair enables manufacturers to boost output and keep pace with the lightning-fast pace of the modern market.