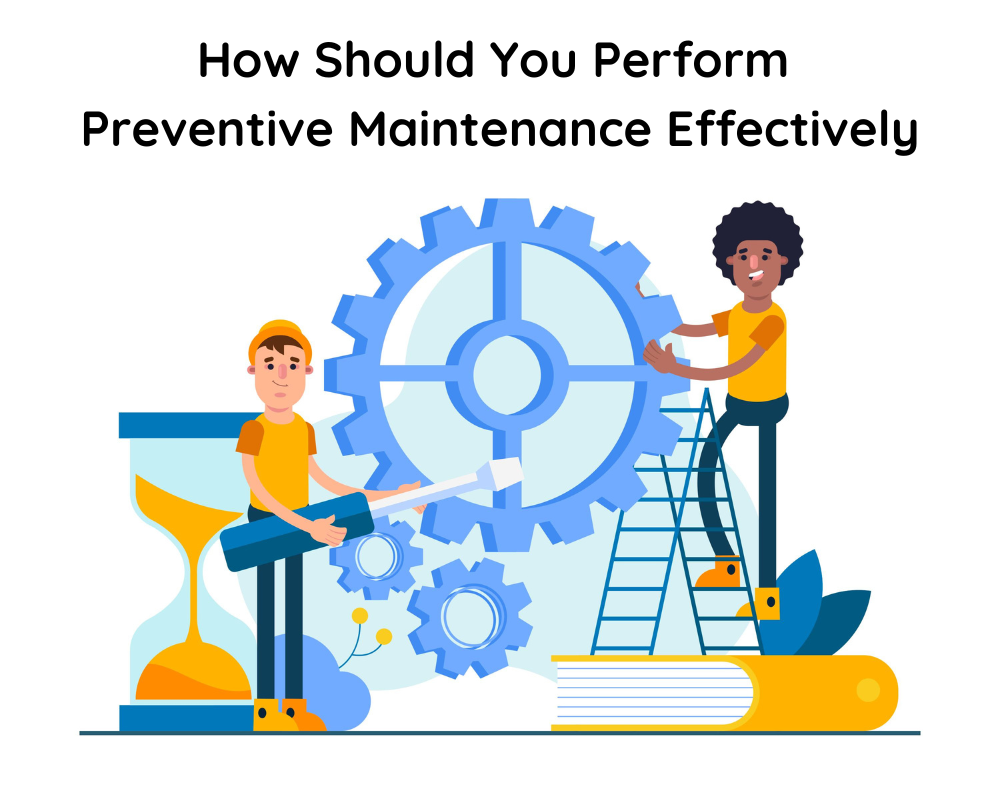
Preventive maintenance is an essential element of a facility maintenance program. Scheduling and performing planned maintenance on plants and equipment can help minimize the risk of unplanned downtime. It also extends the useful life of your equipment and improves operational efficiency. Yet many industrial and plant managers don’t understand the importance of preventive maintenance. As well as how to implement the preventive maintenance task effectively.
By the end of this reading, you will know what preventive maintenance is and why it is essential for your company to keep the facilities running. You will also learn some of the best practices in planning and scheduling preventive maintenance for your plant and equipment.
Let’s dive into how you can perform preventive maintenance in your company!
What Is Preventive Maintenance?
Preventive maintenance is a proactive approach to preventing malfunctions and costly breakdowns in industrial plants and equipment. It includes scheduled inspections of machines. This is to identify potential problems before they become an issue. Preventive maintenance is one of the most important aspects of your maintenance plan. As well as regular cleaning, lubrication, and other maintenance tasks.
This kind of maintenance helps cut down on downtime, extend the life of equipment, and make the workplace safer. Businesses can make sure that their machines are working at their best by planning and scheduling preventive maintenance. It can also reduce expensive repair bills due to unexpected malfunctions.
Preventive maintenance activities can include:
- Regular inspections of equipment
- Regular cleaning of buildings, grounds, and assets
- Lubricating moving parts to reduce wear and tear
- Replacing parts before they expire
- Applying a protective coating to surfaces to prevent corrosion
- Inspecting for signs of physical damage or leaking fluids
- Monitoring for changes in levels of vibration or unusual sounds.
Developing a Preventive and Maintenance Program
A preventive maintenance program needs effective planning and scheduling management. Companies should establish clear goals and objectives to ensure the successful conduct of preventive maintenance. This includes, but is not limited to, the following:
- defining the scope of work for preventive maintenance;
- establishing criteria for preventive maintenance activities;
- setting timelines, and
- Monitor the performance.
Having key personnel involved in the development of the program is essential for the success of the activity. A solid agreement between all those involved in the areas of cost, schedules, resource availability, and quality can help meet the desired outcomes.
It is also important to install technological systems to optimize and track preventive maintenance programs. Software applications can measure performance metrics such as the number of repairs per machine per day, scrap rates, and downtime tracking. It can also track operational effectiveness and help industrial companies improve their processes in real-time. It also helps to make more informed decisions about the preventive maintenance strategy of the company.
How to Plan and Schedule Preventive Maintenance
For organizations that have many assets to manage, planning and scheduling preventive maintenance is key. Managing preventive maintenance activities helps to prevent costly breakdowns and disruptions to operations.
Count the Assets
Asset inventory requires an individual to understand the lifespan of each asset. As well as the factors that may increase or decrease the asset’s life span.
Prioritization of Assets to be Maintained
After making an inventory, it’s important to figure out which assets need maintenance more often than others.
Determining which tasks must be finished first and having a system in place for consistently scheduling these tasks are crucial. This avoids expensive breakdowns and other problems.
Maintenance of Equipment Intervals
Once you have a full understanding of your equipment and the frequency of maintenance required for each, you can then determine the ideal preventative maintenance intervals.
Organizations need to create detailed processes and procedures for regularly scheduled preventive maintenance. This will ensure that there is no confusion over what needs to be done when, and by whom.
Inspect Equipment and Clean it Regularly
Regular inspections are key to extending the life of your plant and equipment. Keeping a record of any issues or changes can help managers predict when an item may need to be repaired or replaced.
Regular cleaning is essential for keeping your plant and equipment running smoothly. Dirt, debris, and other materials can create friction and cause malfunctions that could lead to expensive repairs down the line.
Adjust Controls
Adjusting controls as needed, such as thermostats, air intakes, and valves, can help ensure correct temperature settings, optimal energy efficiency, and proper ventilation are maintained throughout the entire facility.
Tracking and Monitoring Equipment Performance
Businesses should monitor and track their plants’ and equipment’s performance. It is essential for their preventive maintenance program. Monitoring and monitoring the performance of each item to verify that it is running at peak efficiency. Methods of monitoring performance to find areas for improvement should be included in the preventive maintenance program. This is to maximize equipment efficiency.
Best Practices for Achieving Effective Preventive Maintenance
Doing preventative maintenance correctly necessitates keeping a close watch on industry best practices. Following the following stages will help you create an effective strategy that suits the demands of your industry and company:
- Develop preventative maintenance tasks: Start by creating preventative maintenance tasks that identify safety-related activities. As well as preventive and predictive maintenance activities and lubrication of moving parts. Also the routine inspections and other activities.
- Establish preventative maintenance inspection checklists: Create preventative maintenance checklists. This is to ensure all the appropriate equipment is inspected regularly. That all potential problems are caught before they become major issues.
- Bring the right supplies into inventory: When performing preventive maintenance tasks on-site, make sure that you have the necessary supplies (parts and materials) readily available. Instead of having to wait for parts or order them from outside vendors.
- Schedule regular training sessions: Provide consistent preventative maintenance training for all employees. and demand certifications from persons assuming such obligations.
- Adhere to a consistent plan: To achieve the greatest levels of occupational safety, planned preventative maintenance must follow a consistent process. In order to decrease downtime across the production processes, there should also be a reliability audit.
Industrial organizations will be able to take the necessary actions to limit the risk of expensive downtime with the assistance of the best practices listed above. Meanwhile, they are improving the performance of their equipment via preventative maintenance.
Conclusion
Preventive maintenance should be performed routinely to ensure the upkeep of industrial plants and equipment. This is to ensure that they remain in an optimal condition at any time. Planning and scheduling preventive maintenance effectively is essential for minimizing disruption and downtime. This is essential in achieving cost efficiency.
Organizing and executing preventive maintenance can be a complex process. With the right strategy, it can become a streamlined and seamless operation. Taking a systematic approach to planning and scheduling can help make preventive maintenance easier. As well as making it a more effective task for your company.
Industrial managers should utilize modern maintenance technologies and ensure their team is up to date on the latest industry best practices.